Make a Reasonable Choice: Factors to Consider When Buying a Plasma Cutter
If you’re a metallurgist or welder, you probably know that the equipment you use in your working processes plays a huge role in the quality of your final products. A plasma cutter is one of the tools that can make or break your work. Plasma cutters are used to make precise, easy and less time-consuming metal cuts. So whether you’re buying your first plasma cutter, or you’re looking for the best plasma cutter money can buy to upgrade your current setup, choosing the right one can be a process. This is due to the fact that many new technologies have become available in the past few years, so plasma cutters have gotten their fair share of improvements. Also, different manufacturers offer different features and qualities, so it’s easy to get confused. Without further ado, here’s what you need to pay attention to.
Important Factors to Consider
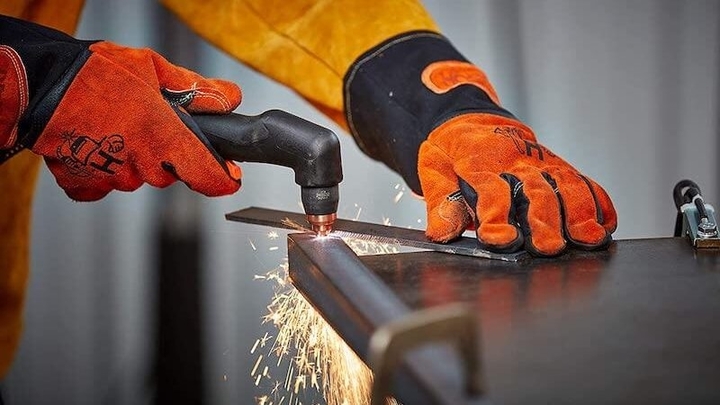
First and foremost, let’s talk about the key factors to consider when shopping for a plasma cutter: duty cycle, cutting speed and performance, input power/electrical output, built-in inverter, portability, and availability of parts and consumables.
Duty Cycle
The duty cycle of a plasma cutter is arguably the most important factor to consider. It refers to the product’s ability to operate safely, and it’s determined by the number of amperages the tool requires. The duty cycle is expressed in percentages, and as a general rule of thumb, a tool with a lower percentage will run for shorter periods than a tool with a higher percentage. More amperage equals a higher duty cycle. Whether you actually need a plasma cutter with a high duty cycle will depend on your processes and how frequently you’ll use the tool. A 50% duty cycle is more than enough in most cases, but if you intend on cutting for longer periods, you’ll need a larger cutter and use it at a lower amperage level. Besides how long and often you’ll use the cutter, you should consider the thickness of the metals you’re going to cut. You want your plasma cutter to be capable of cutting the thickest metals you work with.
Cutting Speed and Performance
These two things can’t be overlooked, as they’ll play a crucial role in what you can, and cannot cut. That being said, the thickness of the materials you work with, plus your desired cutting speed will determine the ideal parameters you should look for. There are three types of cutting quality for plasma cutters – rated, quality and severe cuts. Rated cuts provide the highest-quality cuts, but they’re generally used for mild and thin steel. They also provide max cutting speed, and result in smooth cuts. Quality cuts are used for cutting through thicker metals, and they take longer to cut. Lastly, severe cuts can cut through the thickest of metals, but they provide the least clean cuts. As a result, you’ll have to clean it up after the fact.
Input Power and Electrical Outlet
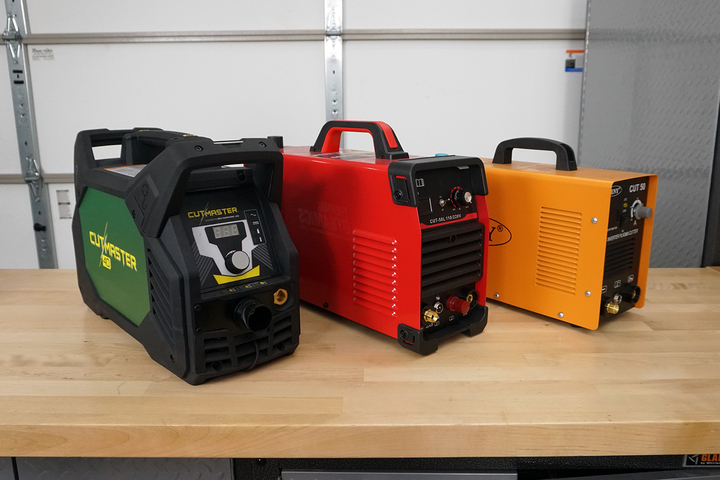
Consider the type of electrical outlets you have. This is especially important if you’re buying the tool from overseas, the US, specifically. Does the cutter run on 110V, 120V or 220V? Most run on either 110V or 220V, while there are a few models that can handle both. The ability to change the voltage is considered a feature. Further, consider the amperage rating. For cutting thin materials, a 25 amp cutter will suffice. For cutting medium-thickness metal, a 40 amp cutter is needed. And for cutting thick metals, you’ll need a cutter with at least 80 amps. To get the most out of any plasma cutter, you should use a separate circuit than you do for other tools.
Built-In Inverter
Plasma cutters that feature a built-in inverter come at a significantly higher price. However, if you work in a remote spot with no power, you might have problems using a conventional cutter. If that’s the case, the inverter will provide a lot of value. Inverters allow you to transform DC power and feed it through a high-frequency transistor. As a result, a cutter with a built-in inverter is likely to be more portable as well.
Portability
For some users, portability is more important than for others. Plasma cutter tools can be used for a variety of applications, and they might need to be moved from one place to another. If that’s the case, the unit you buy should be easily portable and have in-built features that make transportation easier. Size and weight also play a role, and having a built-in compressor and inverter make the units more compact. Some units feature built-in storage you can carry consumes in.
Replacement Parts and Consumables
You should make sure the unit you buy has widely available and affordable replacement parts and consumables. Some of the most popular consumables include electrodes, shields, swirl rings, nozzles and retaining cups. The nozzle and electrodes need to be frequently replaced, so make sure you account for their price when buying a unit.